- Modern Aircooled 4-Cylinder Aircraft Engine
Using Contemporary Engine Technology -
126 HP, 186-pound, O-200 Replacement
NOTE: All our Products, Designs and Services are SUSTAINABLE, ORGANIC, GLUTEN-FREE, CONTAIN NO GMO's, and will not upset anyone's precious FEELINGS or delicate SENSIBILITIES.
STATUS UPDATE: MARCH 2022
CERTIFICATION TESTING of the PRODUCTION ENGINE CONFIGURATION to ASTM STANDARDS for LSA AIRCRAFT IS CURRENTLY UNDER WAY.
Part of that testing required a sustained full power run at 3200 RPM. During that dyno-run, the engine was measured at 141 (honest) HP.
NOTICE:
THE INFORMATION CONTAINED HERE IS ALL I KNOW ABOUT THE PROJECT.
THE CLIENT COMPANY DOES NOT REGULARLY UPDATE ME ON THE PROGRAM DETAILS.
THE ENGINE DESCRIBED HERE WAS DESIGNED AND BUILT BY EPI, Inc. FOR AN UNDISCLOSED CLIENT COMPANY AS DESCRIBED BELOW. THE CLIENT COMPANY OWNS ALL THE CALCULATIONS, CAD MODELS, DRAWINGS, PROCESSES, COMPONENTS, MATERIALS, TOOLING, AND PRODUCTION RIGHTS, AND ALL THE INTELLECTUAL PROPERTY REPRESENTED THEREIN.
THE COMPANY IS ACTIVELY TESTING THE PROTOTYPE and PRODUCTION CONFIGURATION ENGINES AND IS DEVELOPING THE MEANS TO PRODUCE IT IN VOLUME AT LOW COST.
IT IS A SIGNIFICANT EFFORT IN TERMS OF BOTH TIME AND MONEY TO PROGRESS FROM THREE PROTOTYPE ENGINES ON A TEST STAND TO ESTABLISHING A FULL ENGINE PRODUCTION CAPABILITY.
THE COMPANY IS PLANNING TO ANNOUNCE THE ENGINE TO THE PUBLIC AS SOON AS:
- THEY ARE SATISFIED THEY CAN VOLUME-PRODUCE IT TO THEIR HIGH QUALITY STANDARDS, and
- THEY ARE SATISFIED THE PRODUCTION VERSION MEETS THEIR HIGH RELIABILITY STANDARDS.
----> NOTE: CERTIFICATION TO FAR PART 33 IS NOT UNDER CONSIDERATION <----
I regularly get emails asking when this engine will be available for retrofit onto their Cessna-150 or some other Part-23-certificated airframe.
Please understand that it is very difficult (impossible in most FSDO jurisdictions) to get an airworthiness certificate for the installation of a non-certified engine into a certified airframe.
(See THIS DETAILED DISCUSSION for further information on that subject.)
One of the major factors in this decision is that the cost to obtain a Part-33 type certificate for a new engine is measurable in dollar numbers that have six zeroes in the number (as in "5,000,000" for example).
And once the ENGINE type certificate is obtained, the company must next obtain a PRODUCTION certificate (FAR 21.121 through 21.130 and FAR 23 Subpart E) for the engine, which costs yet an additional boatload of money.
After obtaining those two certificates for the engine, the company would have to obtain an STC for the installation into EACH DIFFERENT airframe - - - MORE BOATLOADS OF MONEY.
When all that investment is analyzed in comparison to the POTENTIAL profit to be made from selling engines into that VERY LIMITED marketplace, the decision becomes a "no-brainer".
THEREFORE, PLEASE UNDERSTAND THAT THIS ENGINE WILL BE A PRODUCT THAT FULLY
SATISFIES THE ASTM SPEC FOR LSA ENGINES AND THUS IS SUITABLE ONLY FOR
LSA AND FOR EXPERIMENTAL-HOMEBUILT CATEGORY AIRCRAFT.
INTRODUCTION
In early 2013, the CEO of a well-known aircraft component company contacted EPI to inquire about the feasibility of designing and developing a clean-sheet aircooled engine to replace the ancient, underpowered, and overpriced Continental O-200.
Those discussions resulted in the commencement of an intensive engine design program at EPI, with consultation and review input from the chief engineer at a well-known and respected supplier of PMA engine parts for Continental and Lycoming engines.
POWER COMPARISONS
The engine that resulted from this program is a 200 cubic inch, horizontally-opposed 4-cylinder engine which is a bolt-in replacement for the O-200 (although a different motor mount will be required to clear the accessories on the back of the engine), and which (as of current dynamometer testing) produces 126 HP at 2700 RPM, corrected to accepted sea-level, standard conditions (59°F ambient temperature and 29.92 in-hg ambient pressure). The prototype engines weigh 191 pounds, but there is a weight-loss program underway which looks as if it will reduce the weight by an additional 5 pounds with no effect on reliability or power output.
Although the power output of this new engine is 26% greater than the ADVERTISED 100 HP of the O-200, our engine, in reality, produces over 32% more power than the O-200.
We say that because, of the several brand-new O-200-D engines (advertised at "100 HP" ) that we have tested on the same dyno facility, NONE has ever exceeded 95 HP (corrected to the same 59°F, 29.92" standard).
Please note that this apparent discrepancy is NOT due to any inherent misrepresentation on the part of the certified engine manufacturer. Instead, the discrepancy arises from a tainted correction procedure which the FAA allows to be used on all reciprocating engines certificated under FAR-Part-33. If the dyno-tests for this new EPI engine were corrected to the same biased FAA standards for certified engines, the result would be 134 HP. (We prefer to advertise actual, standardized power measurements.)
ENGINE DESCRIPTION
The following picture shows one of the prototype engines being built up for a testing session at the client's facility. Of note here are (a) the monolithic aluminum cylinders, (b) the eight cylinder hold-down studs, (c) the extended crankshaft nose, and (d) the electronic ignition coil packs..
Prototype Engine Build-Up
This engine embodies innovative technology and features which provide high output, low fuel consumption, and extremely reliable operation in aircraft service. These features include:
- High strength-and-stiffness crankcase cast from a premium heat-treated alloy;
- Optimized multi-gallery lubrication system with full-flow spin-on filter, oil cooler ports, and integrated oil thermostst;
- Custom-designed high-strength, high-stiffness crankshaft that has an integrated 4-inch propeller extension, allowing better cowling aerodynamics;
- High-strength H-beam connecting rods;
- Pistons forged from a high-strength aluminum alloy (which was developed by Rolls-Royce for aircraft engines) and tailored specifically for the air-cooled cylinders on this engine;
- High-pressure oil jets to cool the underside of the pistons;
- Alloy-steel camshaft with custom-designed lobes, tailored to produce high opening and initial closing velocity (for more area under the lift curve) together with low seating velocity (for prolonged valve and seat life), and which have extremely smooth first, second and third derivative profiles;
- Hydraulic roller cam followers;
- Stiff pushrods;
- Very strong and stiff rocker arms on needle-bearing trunnions;
- Intake and exhaust valves made from very-high-temperature and very-high-strength alloys;
- High-grade aluminum-bronze valve guides for long life and fast heat dissipation
- High-strength progressive "beehive" valvesprings which dramatically reduce sensitivity to vibration excitations from higher harmonics of the lift and acceleration profiles;
- High-flow intake and exhaust ports;
- Combustion chambers with high-squish and rapid flame-front propagation properties;
- All sealing between static components done with O-rings;
- High-grade fasteners throughout;
- Unusually-high heat-rejection capabilities engineered into the cylinders and heads;
- Contemporary electronically-controlled fuel injection and ignition, with optimized maps;
- A custom-designed redundant ECU which will be certified to existing standards;
- .......and MORE.
Many of the internal components are purchased from manufacturers that (a) have track-records of producing engine parts and subsystems that survive brutal testing scenarios and (b) that have robust and proven QC systems in place.
Unfortunately, the vendor we initially selected to do the crankcase and cylinder machining (which, BTW, came highly recommended and was alleged to be producing components suitable for certified engines) proved to be incapable of demonstrating the remotest comprehension of basic machining skills and quality standards {never mind aircraft quality standards}.
That (very expensive) experience convinced the client to move as much of the critical manufacturing processes as is practical to in-house facilities in order to assure the highest quality standards.
INTERNAL COMPONENTS
The following pictures show a few of the internal components.
Finished High-Strength, High-Stiffness Crankcase Half (Port Side)
Finished Crankcase Half With Bearings and Roller Lifters In Place (Starboard Side)
Prototype Camshaft Being Measured for Lift, Velocity, Acceleration and Jerk Profiles
Piston, Pin and Connecting Rod
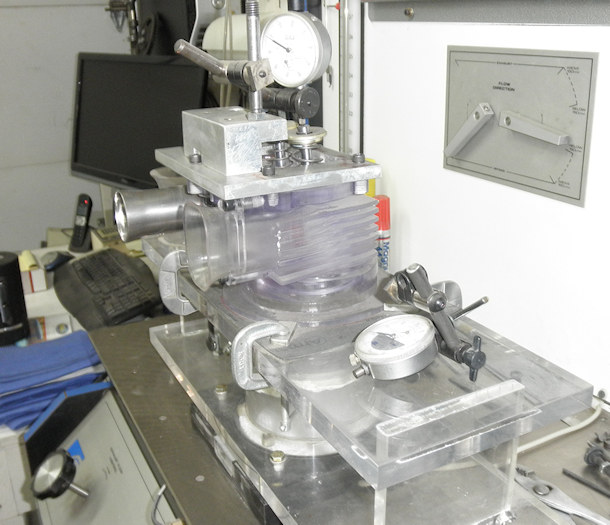
Flow-Developing Rapid-Prototype Head
Finish-Machined Monolithic Aluminum Cylinder
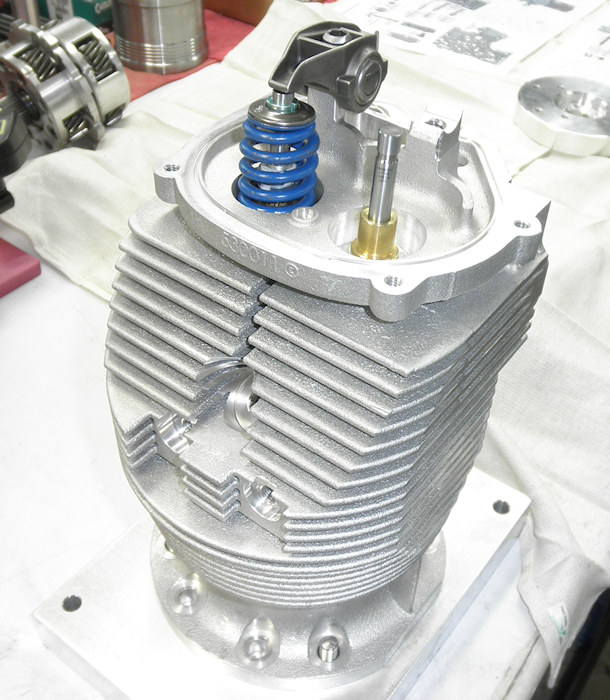
Cylinder Build in Progress
INTERNAL STRESS STUDIES
This engine was completely designed in 3D-CAD (SolidWorks). We subjected all critical components to extensive FEA in order to maximize reliability and to provide sufficient strength margins for future developments, including a 160+ HP turbocharged version with a constant-speed hydraulic propeller.
The following pictures show a tiny sample of the many FEA studies done on the crankshaft, pistons, rods and wristpins. The first picture shows one of the many cases run on the crankshaft. In this case, we applied combined overloads from all major sources (117% of peak combustion pressure, 125% of peak inertial loads, 125% of maximum possible propeller thrust, and the gyroscopic load generated by a propeller with 125% of the mass moment of inertia of the service propeller turning at 2700 RPM under the influence of a 2.5 radian-per-second pitch (or yaw) rate. In this case, the max stress was a modest 56 ksi, located (as expected) in the rod journal fillet radii.
Crankshaft at 12° ATC with 1400 PSI Combustion Pressure,
Plus 125% Max Inertial, Gyroscopic and Thrust Loads
Piston, Pin and Rod with Asymmetrically-Applied Peak Combustion Pressure
The first run of the first prototype engine occurred at the client's facility on 23 November 2016, and was very successful. After careful break-in and thorough in-process evaluations (spanning several weeks), the engine was finally subjected to an extended run at full power. During that run, it produced 126 corrected HP at 2700 RPM using fuel and spark maps that had not yet been optimized. Further increases in peak HP are expected as development continues.
Watch a short movie of the FIRST RUN OF THE ENGINE (23 Nov 2016) and the FIRST FULL POWER TEST HERE.
VIDEO : FIRST RUN OF ENGINE - CLICK the PICTURE
SUMMARY
As with any completely new engine, we have experienced some minor problems. The company is addressing those problems in preparation for an extended full-power dyno-testing program, followed by in-flight testing as soon as the targeted reliability has been confirmed by ground-testing and teardown inspections.
The company is also developing the manufacturing facilities that are required to implement a full scale engine production capability
The really-great news about this engine is that the TARGETED sales price is less than half that of a Continental O-200-D.